We live in a very “international” age where it’s pretty impossible to live in any part of this country and not have access to information about a plethora of subjects and issues spanning the globe. And whether or not you pay much attention to it all or a little bit, at some stage you’re bound to come across sign posts for key factors that essentially impact Australians and their economy.
For example, perhaps up until this year you had paid little to no attention to where the clothes on your back were actually produced and then there was the absolutely devastating building collapse of the clothing factory in Bangladesh.
Perhaps this tragedy has highlighted some significant areas for consideration including what is the best production practice for Australian fashion houses. This brings us to print runs produced off shore, predominantly in China but increasingly in Korea and India, compared to printing on our own sunny shores. Should we be pushing for one over the other or is there a happy medium that can be forged with cooperation from members of the TCFA industry bodies and government?
Clearly price point is a huge factor and although the minimum wage for factory workers in these countries is well below what we would consider acceptable for ourselves, if we were to take away their source of income altogether by ceasing production completely, what does that do to their livelihood? And yet to support innovation and growth within Australia for both screen and digital printing is to continue to promote our own economic growth with an increased work force and encourage companies to stay local.
You can’t deny that China in particular has a rich history of fabric innovation being the first to cultivate and produce silk. Neither can you dismiss India and her surrounds for their impact on international printing trends and practices. But it would be great if right here in our own backyard we were given the opportunity to establish a stable and reliable fashion printing industry on a large scale.
The printing that is currently offered here in Australia has some key advantages and should be taken advantage of. Companies can deal directly with printers giving them a greater amount of control from initial strike off to full bulk runs. This in turn reduces time pressures by limiting the back and forth waiting for shipments or time zone constraints. Minimums are generally lower which means sampling can be produced with a lower risk and greater flexibility of having multiple print styles. And on an environmental note, the freight back and forth overseas is greatly reduced lowering emissions.
So keep up to date on all that international news, live globally, but support Australian industries, print local, print with Digital Fabrics!
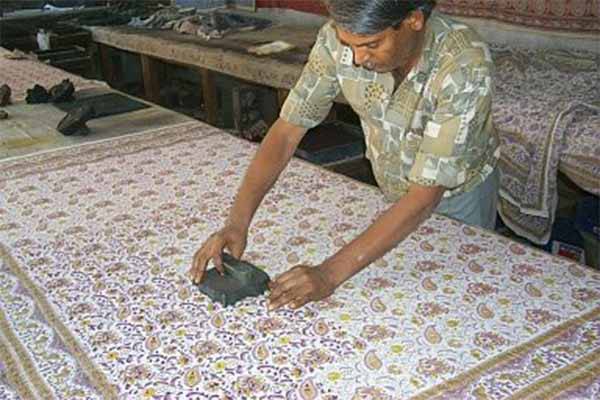
image from : www.grant.org/plewins/india2000/Artists/block.html
Block printing on cloth for the clothing market has been in circulation since the time of the Ancient Egyptians. India and China both too have rich histories in printing cloth to be worn as garments. In Peru, prior to the settlement of the Spanish in the sixteenth century, the Incan society had a highly developed method of printing. In the seventeenth century, with high society in Europe driving fashion trends, the popularity of hand painted and block printed calico from India increased rapidly. The superiority of fine fabric and bright designs from India lead to their ban in France and England until they were eventually lifted in 1759 as the European mills perfected the art of copies.
Mid eighteenth century saw the start of the industrial revolution and the introduction of new technologies. Block printing was replaced by mechanised roller printing. Mass produced textiles for both the home and for fashion began. Although the high volume of printed fabric tended to lessen the quality of the designs, it also made them far more affordable which in turn showed an increase in middle to lower class people wearing printed fashions.
Flatbed screen printing was introduced in the 1930’s with improvements in stencil application throughout the years. Fibre developments and metal verse wooden screens also saw dramatic improvements to the accuracy and multi coloured designs printed. The 1950’s mechanised flatbed printing and in 1962 rotary printing was introduced.
Digital textile printing in the late 1980’s radically changed textile design and production for the fashion industry. Dye sublimation printing furthered this impact in the 1990’s. The creative possibilities, aesthetics and photographic replication have considerably increased a designer’s choice for quality printed fashion textiles. This digital fabric printing technology is constantly being improved and modified; opening doors to all areas of innovative fashion design the world over.
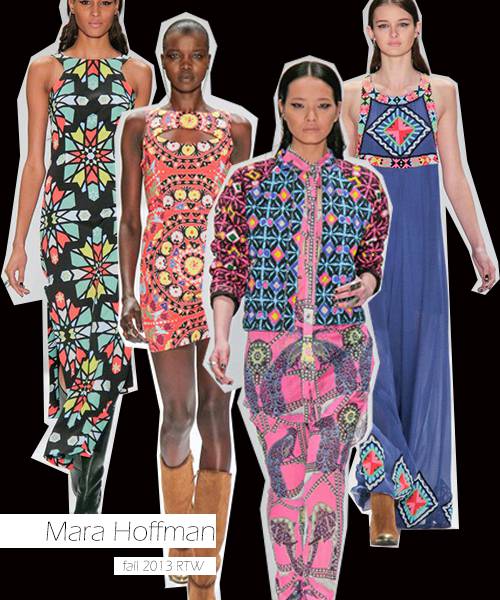
Take a closer look in our other article on digital fabric printing prospects.
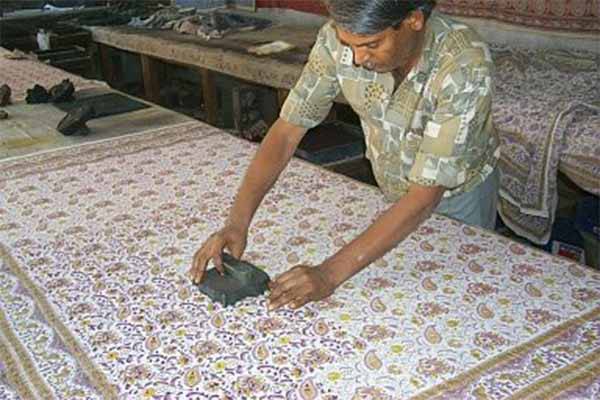
image from : www.grant.org/plewins/india2000/Artists/block.html
Block printing on cloth for the clothing market has been in circulation since the time of the Ancient Egyptians. India and China both too have rich histories in printing cloth to be worn as garments. In Peru, prior to the settlement of the Spanish in the sixteenth century, the Incan society had a highly developed method of printing. In the seventeenth century, with high society in Europe driving fashion trends, the popularity of hand painted and block printed calico from India increased rapidly. The superiority of fine fabric and bright designs from India lead to their ban in France and England until they were eventually lifted in 1759 as the European mills perfected the art of copies.
Mid eighteenth century saw the start of the industrial revolution and the introduction of new technologies. Block printing was replaced by mechanised roller printing. Mass produced textiles for both the home and for fashion began. Although the high volume of printed fabric tended to lessen the quality of the designs, it also made them far more affordable which in turn showed an increase in middle to lower class people wearing printed fashions.
Flatbed screen printing was introduced in the 1930’s with improvements in stencil application throughout the years. Fibre developments and metal verse wooden screens also saw dramatic improvements to the accuracy and multi coloured designs printed. The 1950’s mechanised flatbed printing and in 1962 rotary printing was introduced.
Digital textile printing in the late 1980’s radically changed textile design and production for the fashion industry. Dye sublimation printing furthered this impact in the 1990’s. The creative possibilities, aesthetics and photographic replication have considerably increased a designer’s choice for quality printed fashion textiles. This digital fabric printing technology is constantly being improved and modified; opening doors to all areas of innovative fashion design the world over.
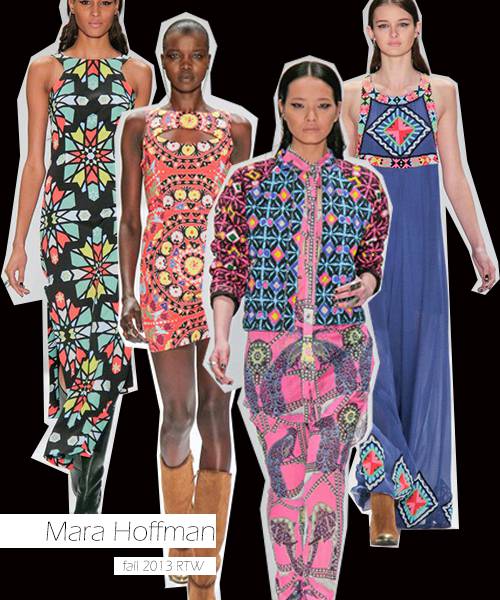
Take a closer look in our other article on digital fabric printing prospects.
Fashion prints are as trend driven as colour and garment style. Fashion prints are becoming an increasingly utilised tool in a fashion designer’s tool kit. Therefore although the following is a general run down of the various types of fashion prints, depending on the season and year, some maybe more popular than others.
Floral – associated with any plant form depicted whether it be a flower bud or tree. There are names descriptive of the scale of the floral such as Liberty or the style such as Ditsy.
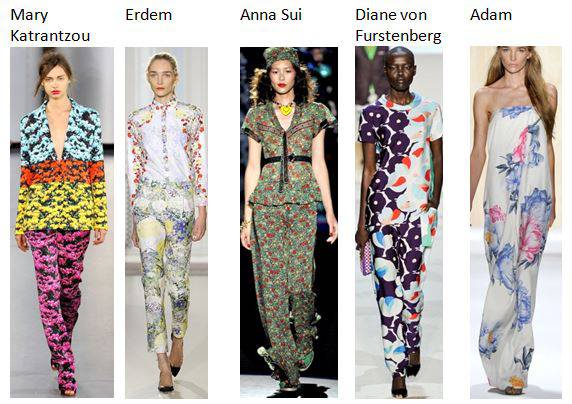
Geo – Geometric prints range from colour blocking random shapes to the tessellating patterns inspired by Islamic art. Geo prints can also fall under Abstract or Graphic.
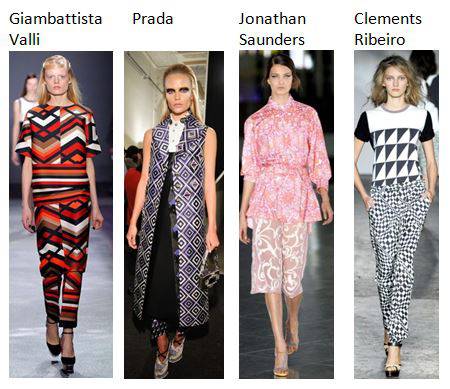
Graphic/Abstract – Abstract is used to describe unrecognisable forms and motifs, mostly because they cannot be described any other way. Graphic is descriptive of the boldness of a print. Refers to predominantly modern designs and sometimes goes hand in hand with another of the types listed here i.e. Graphic Floral.
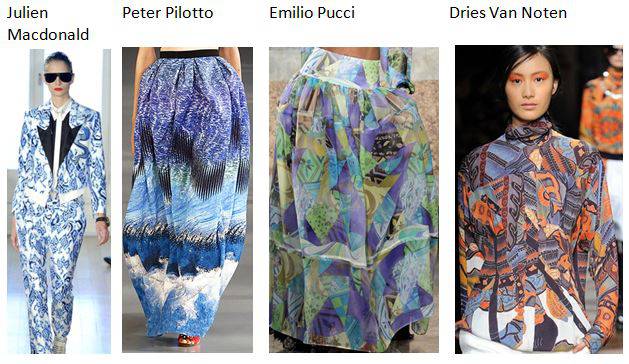
Animal/Skin – Printed replicas of various animal skins not necessarily the full body of the animal itself i.e. leopard, snake, alligator, zebra etc.
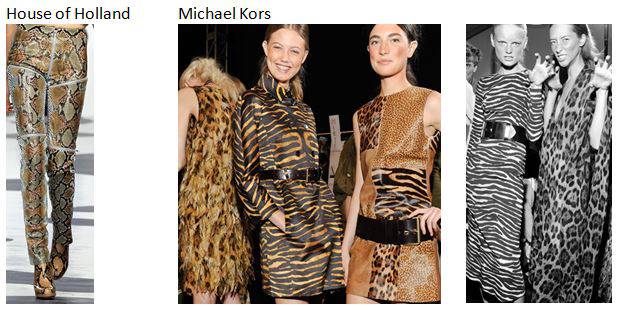
Conversational – Recognisable images such as everyday objects and animals generally taken out of familiar context or placed in conjunction with out of context images i.e. human legs carrying houses. Often ‘cartoon’ in rendering and with a whimsical feel, also called novelty prints.
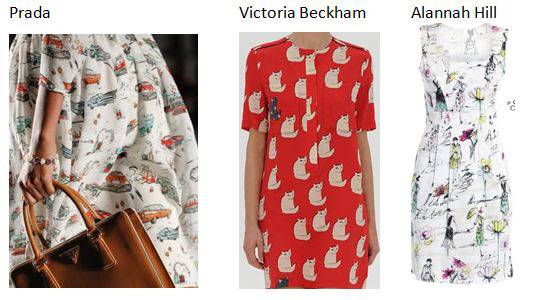
Fashion prints are as trend driven as colour and garment style. Fashion prints are becoming an increasingly utilised tool in a fashion designer’s tool kit. Therefore although the following is a general run down of the various types of fashion prints, depending on the season and year, some maybe more popular than others.
Floral – associated with any plant form depicted whether it be a flower bud or tree. There are names descriptive of the scale of the floral such as Liberty or the style such as Ditsy.
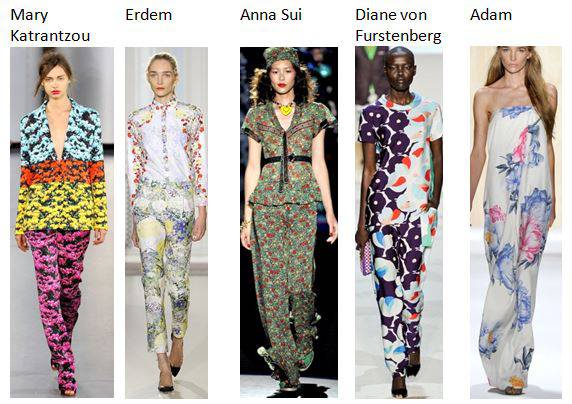
Geo – Geometric prints range from colour blocking random shapes to the tessellating patterns inspired by Islamic art. Geo prints can also fall under Abstract or Graphic.
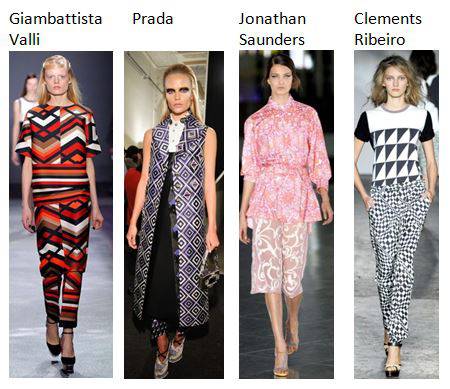
Graphic/Abstract – Abstract is used to describe unrecognisable forms and motifs, mostly because they cannot be described any other way. Graphic is descriptive of the boldness of a print. Refers to predominantly modern designs and sometimes goes hand in hand with another of the types listed here i.e. Graphic Floral.
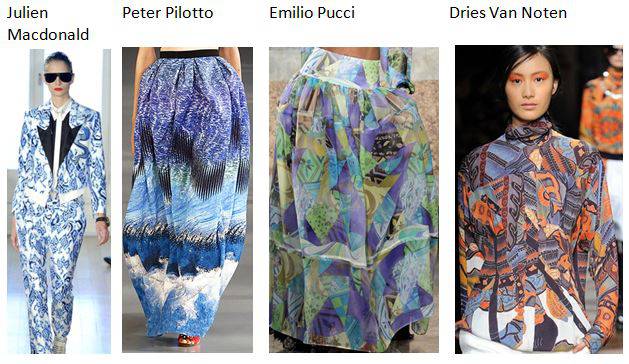
Animal/Skin – Printed replicas of various animal skins not necessarily the full body of the animal itself i.e. leopard, snake, alligator, zebra etc.
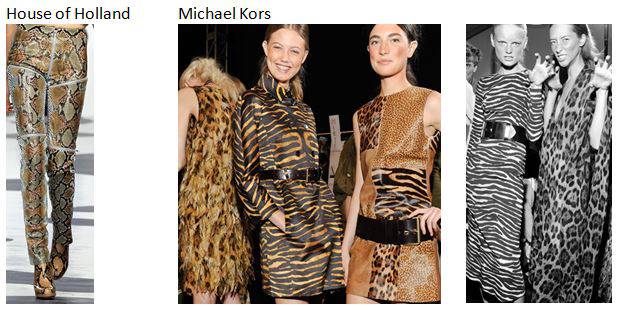
Conversational – Recognisable images such as everyday objects and animals generally taken out of familiar context or placed in conjunction with out of context images i.e. human legs carrying houses. Often ‘cartoon’ in rendering and with a whimsical feel, also called novelty prints.
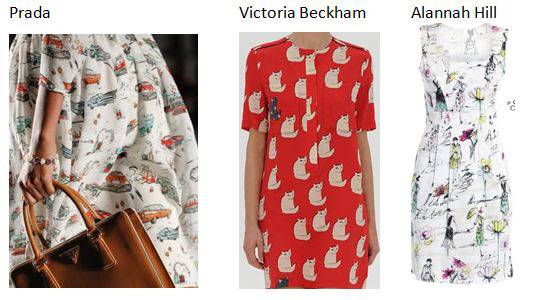